Fallstudien
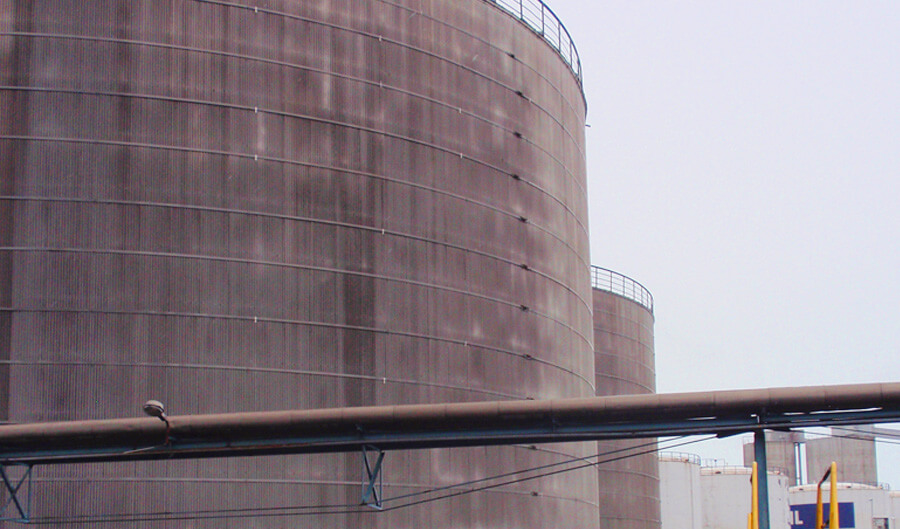
Hohe Produktivität beim Fülldrahtschweißen von LDX-Stahl
„Genauso einfach wie das Schweißen von normalem Edelstahl, aber mit deutlich höheren Abschmelzleistungen als Elektroden. Dies ist das erste Mal, dass wir Fülldrähte für LDX-Stahl verwendet haben, und es war eine durchweg positive Erfahrung.“ Weiterlesen
Dies sagt Peter Nordell, Project Manager bei IVAB in Luleå. Das Unternehmen verwendete Cromacore LDX und Cromarod LDX für die Neuauskleidung von vier Öllagertanks im Hafen von Luleå. Die Tanks waren seit mehreren Jahren leer und brauchten neue Böden, da sie wieder zur Lagerung von Dieselöl für LKAB verwendet werden sollten.
IVAB arbeitete im Winter und Frühjahr 2012 an dem Projekt in Tanks mit einem Durchmesser von 35 Metern und einer Höhe von 20 Metern. Die Böden bestanden aus 3 mm LDX-Stahl, der innen und außen mit dem Mantel verbunden war. Aufgrund der Manteldicke (15 bis 20 mm) war eine Vorwärmung auf 150 °C notwendig und wurde mit einem Miller ProHeat 35 durchgeführt.
Die Fugen zwischen den Bodenplatten waren 5 mm dick und wurden mit Cromacore LDX-Fülldraht zusammengeschweißt. Zum Schweißen auf der Außenseite wurden Cromarod LDX-Elektroden verwendet, da diese eine etwas bessere Beständigkeit gegen Witterungseinflüsse aufweisen.
LDX schaffte den Durchbruch als Alternative zu konventionellem Edelstahl, da letzterer aufgrund steigender Nickelpreise immer teurer wurde. Aber LDX ist nicht nur günstiger, es hat auch bessere Ermüdungseigenschaften und wird oft in Brücken und ähnlichen Konstruktionen eingesetzt.
„Die Cromacore und Cromarod LDX Schweißzusatzwerkstoffe haben einen höheren Nickelgehalt als der LDX-Stahl, um das richtige Ferrit-Austenit-Gleichgewicht in der Schweißnaht zu gewährleisten“, sagt Per Sundberg, Product Manager bei Elga. „Elektroden sind schon lange auf dem Markt, aber gute Qualität bei Fülldrähten brauchte eine Weile. Mit Cromacore LDX und Cromarod LDX verfügen wir nun über ein komplettes Set an LDX-Produkten, und ich kann mit Zuversicht sagen, dass der beste Fülldraht für das LDX-Schweißen auf dem Markt Cromacore ist.“
Der Auftrag von IVAB für die Neuauskleidung der vier Lagertanks umfasste etwa 3.000 Meter Schweißnaht, so dass die maximale Schweißabtragsrate eine wichtige Rolle bei der Wahl des Produkts spielte.
„Fülldraht bietet höhere Produktivität als Elektroden“, sagt Håkan Pavasson, Vertriebsmitarbeiter bei Elga in Luleå. „Die Abscheidung beträgt volle 87 Prozent im Vergleich zu 60 Prozent bei einer Elektrode, und der Fülldraht erfordert weniger Stopps für den Elektrodenwechsel, was den Fülldraht für IVAB sehr attraktiv machte. Nach einem ersten Test entschieden wir uns für den Fülldraht, und obwohl es unser erstes Mal war, verlief die Schweißung völlig problemlos.“
IVAB ist ein Installations- und Rohrleitungsbauunternehmen, das sich u.a. mit der Wartung in der Prozessindustrie und Ölanlagen beschäftigt. Obwohl der Hauptsitz in Piteå ist, ist das Unternehmen landesweit tätig.
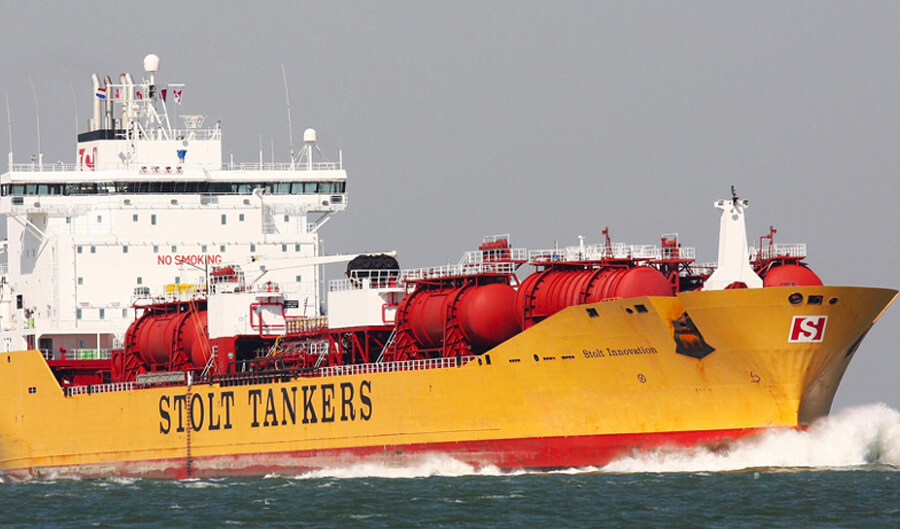
Nichtrostende Tanker
Für die Schiffe der Innovation-Klasse von Stolt Nielsen lieferte Elga nicht nur alle Schweißzusatzwerkstoffe für Duplex-Stähle, sondern stellte auch Schulungsprogramme und Ausbilder zur Verfügung. Weiterlesen
Die Innovation-Klasse umfasst sieben Chemie-Paket-Tanker, die von Danyard gebaut wurden. Ausgestattet mit 46 Duplex-Stahltanks, die von Kofferdämmen umgeben sind, können sie fast alle Arten von Chemikalien transportieren.
Die Innovation-Klasse umfasst sieben Chemie-Paket-Tanker, die von Danyard gebaut wurden. Ausgestattet mit 46 Duplex-Stahltanks, die von Kofferdämmen umgeben sind, können sie fast alle Arten von Chemikalien transportieren.
Schiffe der Innovation-Klasse sind 176 Meter lang, 31 Meter breit und wiegen 37.000 Tonnen. Die Frachtkapazität beträgt etwa 40.000 Kubikmeter.
Die verwendeten Elga-Schweißzusatzwerkstoffe repräsentieren den größten Teil unseres Sortiments für das Duplexschweißen, einschließlich keramischer Zusatzwerkstoffe.
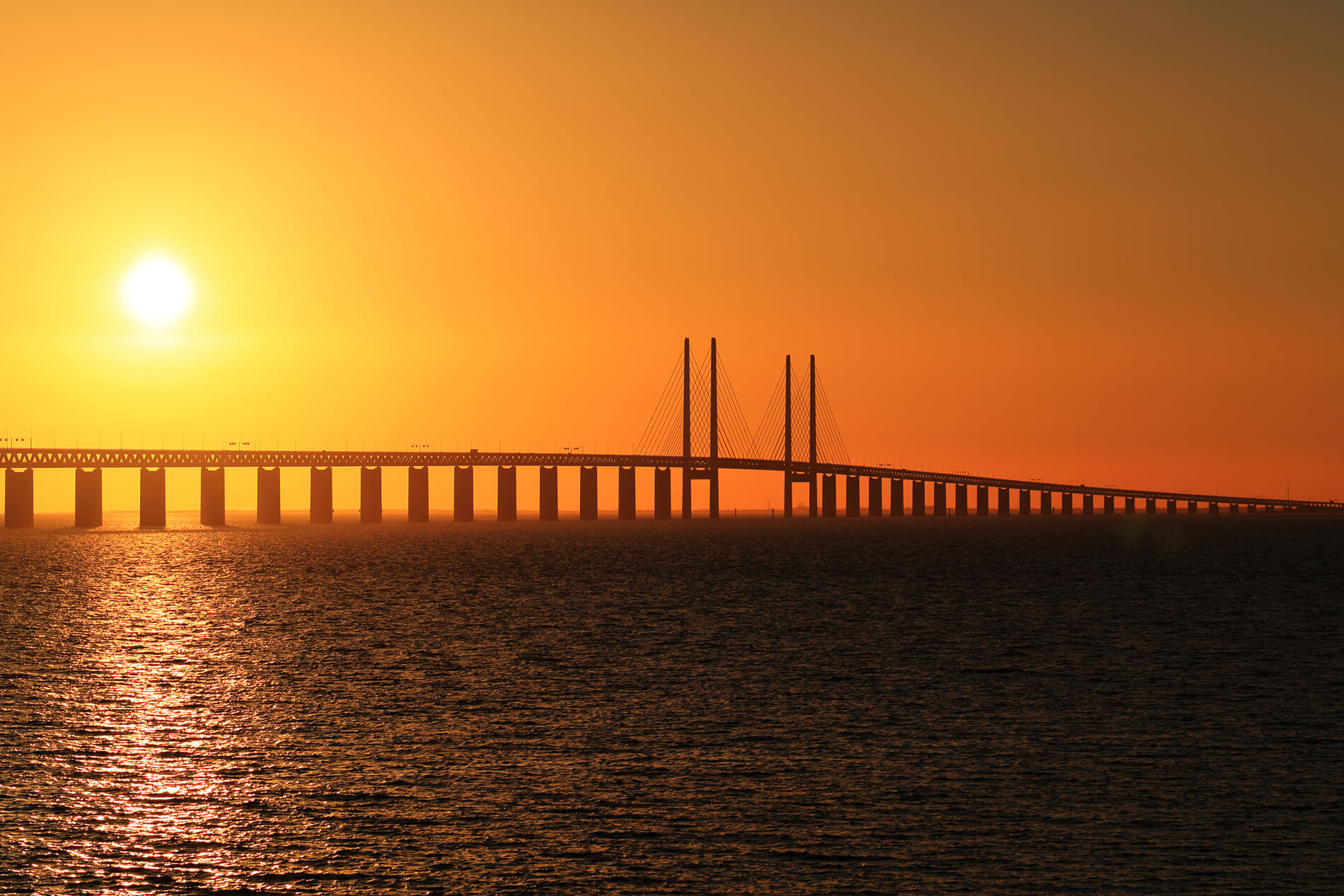
Die Öresundbrücke
Die Öresundbrücke ist die längste kombinierte Straßen- und Eisenbahnbrücke Europas und verbindet zwei große Ballungsräume: Kopenhagen, die dänische Hauptstadt, und die schwedische Stadt Malmö. Weiterlesen
Der Überbau der fast acht Kilometer langen Brücke zwischen Schweden und Dänemark wurde mit Elgacore-Fülldrähten und Rutil-Fülldrähten geschweißt. Der Überbau wurde in Sektionen von der Karlskrona-Werft gebaut und war das größte Stahlprojekt des Unternehmens überhaupt.
Stabilität und Sicherheit
16.000 Tonnen Stahl wurden für acht bis zu 140 Meter lange Stahlelemente verbaut. Die Höhe beträgt elf Meter, die Breite 31 und das größte Teil wiegt rund 2.000 Tonnen. Der Überbau wird von zwei Paaren von 204 Meter hohen Betonpylonen getragen.
Alles in allem bedeutete dies eine Menge Schweißarbeiten, und Karlskrona evaluierte eine Reihe von Lieferanten für Schweißzusatzwerkstoffe, bevor sich das Unternehmen für Elga entschied und Elga mit dieser anspruchsvollen Aufgabe betraute. Die meisten Schweißarbeiten wurden automatisch oder halbautomatisch durchgeführt. Der Grundwerkstoff war hauptsächlich 420 ML und die Anforderungen waren CVN-Werte bei -40°C und CTOD-Tests bei -10°C für Dicken über 50 mm. Hohe Produktivität und einfache Handhabung waren weitere wichtige Anforderungen.
Von der Schulung bis zur Nachkontrolle
Für das automatische und halbautomatische Schweißen wurde Elgacore Metallfülldraht und für das manuelle Schweißen in allen Positionen Elgacore Rutil-Fülldraht verwendet. Der Metallfülldraht wurde bei Bedarf auch für einseitige Wurzelläufe im Tauchverfahren verwendet.
Doch Elgas Aufgabe umfasste viel mehr als die Lieferung von Schweißzusatzwerkstoffen. Dazu gehörten auch die Empfehlung von Schweißparametern, die Vermessung vor Ort, die Schulung der Schweißer und die Produktionskontrolle.
Die Öresundbrücke ist eine doppelstöckige Schrägseilbrücke für kombinierten Straßen- und Eisenbahnverkehr. Sie ist ein Teil der Verbindung zwischen Schweden und Dänemark und wurde am 1. Juli 2000 eingeweiht.
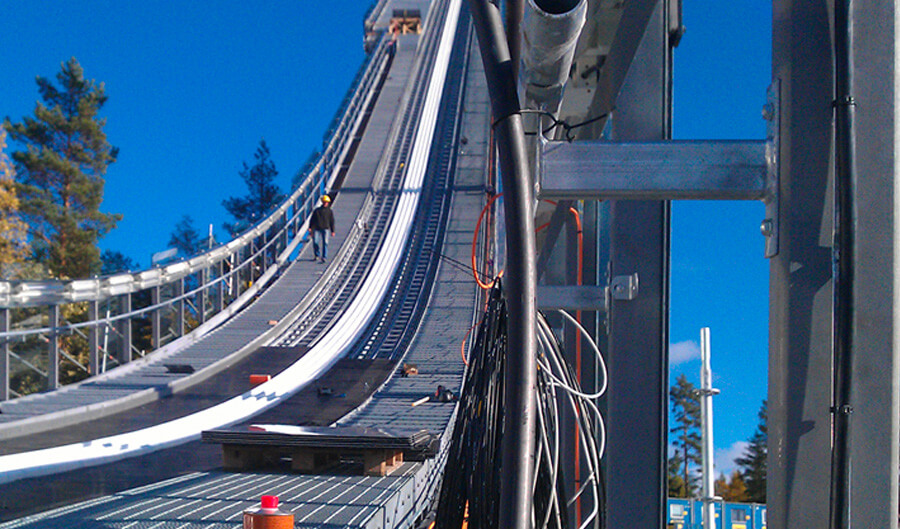
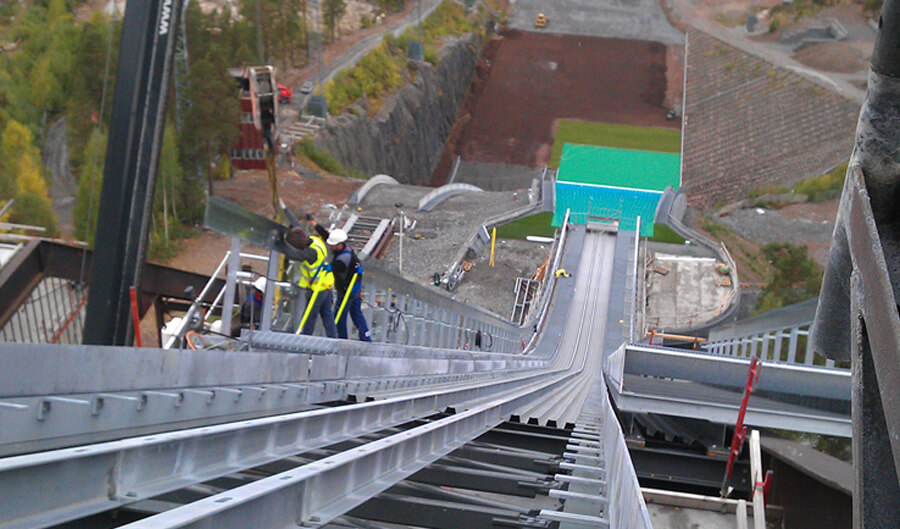
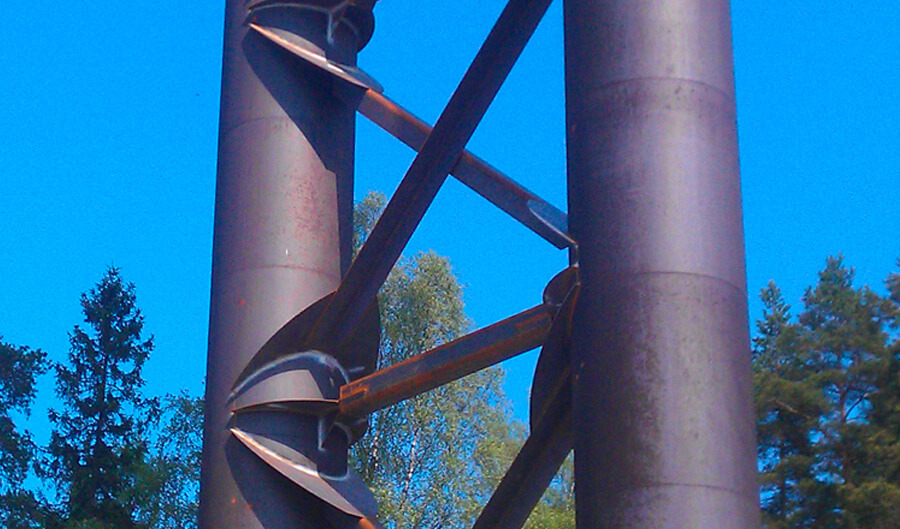
Präzisionsschweißen von oben nach unten
Die Silhouette ist die gleiche. Nur ein geschultes Auge kann erkennen, dass seit Januar 2014 zwei völlig neue Schanzen im Lugnet-Skistadion in Falun bereitstehen. Sjölins Smide in Hudiksvall war etwas mehr als ein Jahr lang mit dem Schweißen der Konstruktion beschäftigt - eine Aufgabe, die viele neue Herausforderungen mit sich brachte: Weiterlesen
2015 fanden in Falun die Skiweltmeisterschaften statt, was der Grund für die beiden neuen Schanzen war. Die alten Schanzen wurden für die Weltmeisterschaften 1974 fertiggestellt und wurden 1993 erneut für die Meisterschaften genutzt. Seitdem hat sich in diesem Sport viel getan, und der Internationale Skiverband (FIS) hat heute ganz neue Maßstäbe für Meisterschaftsschanzen. Der höhere der beiden Schanzen ist jetzt eine K 120 (statt K 115), während ihr kleinerer Begleiter wie bisher eine K 90 ist.
Alles ist neu
„Von den alten Schanzen sind nur noch die Stützen und Seitenträger übrig“, sagt Ulrik Jonasson, Geschäftsführer bei Sjölins Smide. „Alles andere ist neu – der Turm, der Anlauf und Absprung, die Treppen und Handläufe usw. Früher waren die Schanzen eine Mischung aus Holz und Stahl, heute sind es Stahl, Beton und Glas.“
Im November 2012 begann Sjölins mit den Arbeiten, die im Januar 2014 beendet wurden. Dabei wurden fast 200 Tonnen Stahl verbaut.
„Es war wichtig, dass die neuen Schanzen den alten so weit wie möglich ähneln“, fährt Ulrik Jonasson fort. „Der Cortenstahl gab den alten Schanzen eine besondere rostrote Patina, und auch die neuen Schanzen werden ähnlich aussehen.“
Hochpräzise Konstruktion
Da nach den neuen FIS-Regeln alle Meisterschaftsschanzen die gleiche Neigung, das gleiche Profil und die gleiche Absprunghöhe haben müssen, wurde der Anlauf der oberen Schanze erhöht, während die untere Schanze nun länger und flacher ist und die Absprunghöhe geändert wurde. Das Erreichen des exakten Profils stellte hohe Anforderungen an die Messgenauigkeit, was an sich schon eine Herausforderung war.
„Mit der Messung der Schanze haben wir an einem Frühlingsmorgen im März begonnen“, verrät uns Ulrik Jonasson. „Als wir nach einer Pause die Arbeit wieder aufgenommen haben, hat nichts mehr gestimmt. Die Sonne hatte die Konstruktion aufgeheizt und die Messpunkte um mehrere Zentimeter verschoben. Wie verrückt wäre es, wenn es nachts fünfzehn Grad minus und tagsüber plus fünfzehn wäre? Wir waren gezwungen, uns zu entscheiden, nach welchen Messwerten wir arbeiten würden, und uns daran zu halten, egal was passiert.“
Während ein Großteil der Arbeiten in den Werkstätten von Sjölins Smides vorgefertigt wurde, wurde auch ein großer Teil der Schweißarbeiten vor Ort ausgeführt. Um die Montage der neuen Strukturen auf den Resten der alten Schanzen zu ermöglichen, schweißte Sjölins Befestigungspunkte für Schraubverbindungen mit 5 mm Toleranz.
„Ganz oben an den Türmen der Schanzen war das Schweißen nicht viel anders, als wir es gewohnt sind“, sagt Ulrik Jonasson. „Aber die eigentlichen Schanzen sind sehr schräg, so dass es aus sicherheitstechnischer und ergonomischer Sicht eine knifflige Aufgabe war. Immerhin arbeiteten wir manchmal mehr als 50 Meter über dem Boden.“
Elga und Miller
Sjölins verwendete Elga P 48K Elektroden, Elgacore Fülldrähte und Miller XMT 350 Schweißgeräte mit Vorschubkoffern. Sie führten Stumpfnähte und Kehlnähte in allen möglichen Positionen mit 5 bis 20 mm Wurzeltiefe und Materialstärken von 10 bis 40 mm aus. Das meiste war in Cortenstahl, aber einige waren auch in Baustahl. Einige Bereiche wurden für das MAG-Schweißen vor Ort auf der Schanze abgedeckt.
„Es werden immer günstige Materialien angeboten, aber bei unseren Materialien wollten wir absolut sicher sein, und die volle Unterstützung auf dem ganzen Weg genießen“, sagt Ulf. „Elga half uns zum Beispiel mit den richtigen Schweißparametern, WPSs und Schweißplänen für diesen speziellen Auftrag. Es ist wichtiger, effizient schweißen zu können und Nacharbeiten zu vermeiden, als Centbeträge für eine Packung Elektroden zu sparen.“
Vom FIS abgenommen
Unsere Arbeitsmethode wurde von einem externen Prüfer und dem eigenen Prüfer von Lugnet überprüft. Als der FIS die Endkontrolle durchführte, erklärte er, dass die Skispur vorschriftsmäßig und innerhalb der vorgegebenen Toleranzen sei.
Vom Hufeisen zum Stahlbau
Per Sjölin, der 1883 mit seiner Hufschmiede und Schmiede in Hudiksvall begann, würde das heutige Unternehmen sicherlich nicht wiedererkennen. In den 1950er Jahren stellte er das letzte Hufeisen her, und heute arbeiten die 75 Mitarbeiter von Sjölins landesweit an Aufträgen für Tragwerke. In der eigenen Werkstatt werden Schmiedeteile aus Stahl und Edelstahl hergestellt.
FIS Nordische Ski-Weltmeisterschaften
Die Weltmeisterschaften in Falun begannen am 18. Februar 2015 und umfassten Langlauf, Skispringen und Nordische Kombination. Neben den Skisprungschanzen verfügt die Nationale Arena am Lugnet auch über Langlaufloipen, Hallenbad und Arenen für viele verschiedene Sportarten. Der Turm für die größere Skisprungschanze ist für die Öffentlichkeit zugänglich und ist der höchste Aussichtspunkt in Dalarna.