Demystifying Metal-Cored Wires
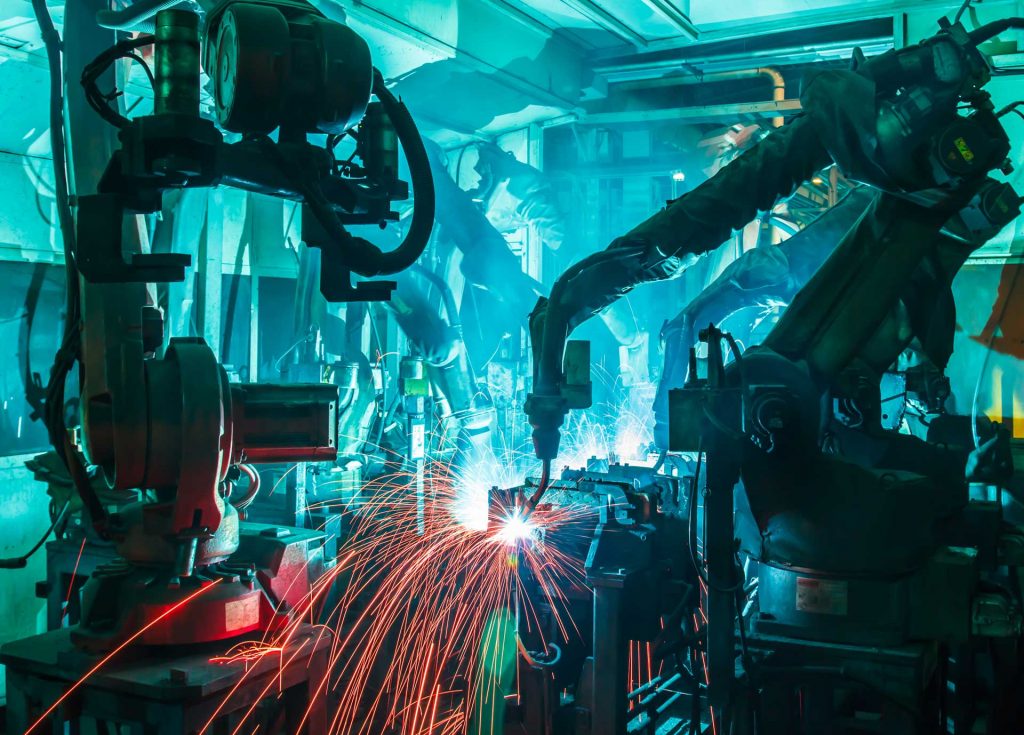
Behind the Technology
Metal-cored wires have a different structure and composition than solid wires, which results in distinctive operating characteristics, too. The wires consist of a hollow metal sheath into which filler metal manufacturers deposit metallic powders and/or alloys, including iron, that are designed to provide characteristics ranging from arc stabilization to higher tensile strengths and more. As a result of this tubular structure, metal-cored wires carry the welding current though the outside metal sheath to the work piece instead of through the entire cross section as with solid wires. At equivalent amperage settings, metal-cored wires also carry higher current densities. The result of both factors is a broad, cone-shaped arc and a wide penetration profile, as well as high burn-off rates that increase deposition rates and can provide faster travel speeds.
Metal-cored wires operate using the „spray transfer“ mode of droplet transfer with high argon shielding gas mixtures (a minimum of 75 percent argon is recommended). Using a constant voltage (CV) power source, the wires are capable of flat, horizontal, vertical-down and overhead welding and can also be used for vertical-up welding, but require a pulsing-capable power source to do so or must be adjusted to the short-circuit mode using a CV power source. Generally speaking, the wires operate at a lower deposition rate in the vertical-up position than flux-cored wires, and at about the same deposition rate as solid wire in the vertical-up position.
Typically, metal-cored wires are available in diameters ranging from 1.0 mm to 1.6 mm.
Identifying the Applications
Like any filler metal, metal-cored wires have applications for which they are better suited than others. They are appropriate for welding on mild, low-alloy and stainless steel, but are not recommended for welding sheet metal. Metal-cored wires work particularly well in the automotive industry for welding components such as chassis and steel wheels, primarily due to their ability to provide a wide bead profile and higher travel speeds. In the manufacturing and fabrication industries, metal-cored wires are well-suited for welding agricultural and heavy equipment, as well as rail cars, mostly due to their ability to weld through rust and mill scale (the fine oxide layer found on hot-rolled steels) — both common factors encountered in these applications. The wires can also aptly weld on 6 mm and thicker plate found in agricultural and heavy equipment manufacturing applications, and are usable for applications in the food and chemical industry, which, conversely, tend to be composed of thinner materials.
In addition, metal-cored wires can often be used as an alternative on certain applications currently using the submerged arc or gas-shielded flux-cored welding processes, as well as on many of the same applications that employ solid wire. These include solid wire applications requiring single-pass welding for welds that are 7 cm or longer, and those applications welded in the flat and horizontal position using the spray transfer mode. On such solid wire applications, companies who choose to convert to metal-cored wires can often increase the wire diameter by one size over a solid wire. Doing so often lets them standardize on a single wire diameter within their facility and allows for welding on a variety of joint sizes and material thicknesses.
Metal-cored wires are typically not recommended for applications requiring a lot of out-of-position welding, but they are good for single- and multi-pass welding using a robotic or automatic welding process. Other applications where metal-cored wires can be used include welding piping or other components where poor fit-up occurs, applications prone to burn-through and those requiring aesthetic bead appearances.
The Attributes and What They Mean
When used with the correct shielding gas mixtures (see previous section) and welding parameters (these are dependent on the application), metal-cored wires provide good weld penetration and high deposition rates, as well as fast travel speeds. Because of the way that these wires carry the welding current and burn off, they create very little spatter, as well as low amounts of slag, and offer very good gap bridging. Certain metal-cored wires offer chemical composition that helps minimize silicon deposits at the toes of the weld, while others are formulated to provide a specific chemistry and/or to increase tensile or impact strengths. Most are very capable of minimizing instances of porosity and providing good sidewall fusion to reduce instances of undercut in the final weldment and rework on defective parts.
On average, metal-cored wires cost more per kg than other filler metals, particularly solid wire. Many companies, however, still select this type of filler metal because of its potential for reducing costs in other areas of the welding operation, particularly in the pre- and post-weld areas. Often the pre-weld areas of a welding operation are used for activities like grinding, sandblasting or degreasing materials in preparation for moving them to the weld cell. In many cases, metal-cored wires can eliminate the need for these activities prior to welding because they can weld through mill scale and rust and they create little spatter. The lack of spatter means companies may be able to eliminate the need (and cost) of using anti-spatter and they can often take welded parts directly for painting without needing a separate cleaning operation beforehand. In certain cases, the elimination of such pre- or post-weld activities can allow companies to reallocate labor elsewhere in the welding operation.
In the welding cell, the fast travel speeds and high deposition rates that metal-cored wires provide can frequently increase productivity, as well. That improvement is most often seen in robotic and automatic welding applications.
What Else Is There to Know?
Metal-cored wire isn’t for every application. In certain ones, however, it can provide the welding performance a company wants and needs. For companies who are considering implementing this technology, it helps to assess the current welding operation and identify whether there are bottlenecks in productivity that exist due to pre- or post-weld activities like grinding or if there are quality issues, such as lack of fusion, spatter or undercut. In some cases, metal-cored wire can help eliminate these problems and improve the efficiency of the welding operation in the process.
Article based on ITW Welding global experience and knowledge.