Properties of Stainless Steels
Ferritic
The main alloy is Cr (~10-30%) and ferritic steels are therefore called chrome steels. They do not normally contain any Ni. They are divided into two groups:
Semi-ferritic
Not ferritic all the way to melting point. (PHT 200-300 ºC and PWHT 700-800 ºC)
Fully ferritic
Ferritic all the way to melting point. (PHT 20 °C, PWHT not necessary). Use small electrodes and low amperage.
There are a few important differences compared to austenitic steels.
• Cheaper to manufacture
• Higher yield strength
• Lower elongation
• Better thermal conductivity
• Not sensitive to restraint cracks
• Not the same weldability as austenitic
• Good machining
Weldability of ferritic stainless steel varies depending upon the composition. Modern grades are reasonably weldable. However, all ferritic stainless steels suffer from grain growth in the HAZ resulting in loss of toughness. Consequently, interpass temperature and heat input must be limited.
Consumables for welding ferritic stainless steels can match parent metal composition or be austenitic.
Martensitic
Main alloys are Cr 11-17%, Ni up to 5% and C up to 0,4%. Martensitic steels are used for tools, but do not have the same hardness or durability as CMn/low-alloy steels used for tools or wear parts.
• May need both PHT and PWHT
• Mostly used as austenitic filler metal
• Hardens in air
• High mechanical properties
Martensitic stainless steels weldability is comparatively poor, and becomes worse with increasing carbon content. It normally requires preheating, well controlled interpass and cooling, as there is a significant risk of cold cracking in HAZ.
Matching-composition martensitic consumables are used when weld metal properties must match parent material. However, to decrease the risk of cracking, austenitic consumables may be used.
Austenitic
For welding applications, it is often desirable to have a small amount of delta-ferrite in the weld metal (310%). These steels do not normally need any post-weld-heat treatment (PWHT). They have about 50% higher thermal expansion compared to ferritic and duplex stainless steels.
Mechanical properties such as yield strength are lower than for ferritic steels.
• Expensive because of alloying element (Ni)
• Good resistance against corrosion (PRE)
• High thermal expansion
• Sensitive to hot cracks
• Good weldability
• Cold hardens when machined
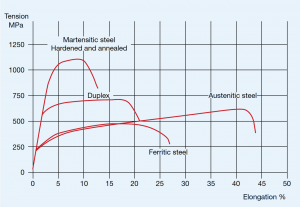
Austenitic stainless steels are the most common and in most cases have really good weldability. Austenitic stainless steels are welded with consumables with a similar or over-alloyed chemical composition compared to the parent metal. Over-alloying is required in the more highly alloyed grades to optimize corrosion resistance.
In some cases there are requirements on fully austenitic weld structures e.g. for higher temperatures.
Duplex
Welding metallurgy has played a key role in the alloy development of duplex stainless steels. In terms of a common engineering material, modern duplex stainless steels are now well established as an alternative to other more general types of stainless steels and for certain applications, even nickel base alloys.

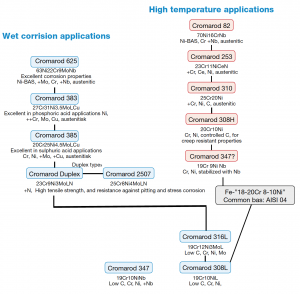
Duplex grades are readily weldable by all commonly used processes such as SMAW, FCAW, GTAW, BMAW, SAW and a large variety of joint designs. When planning welding operations, it is therefore of paramount importance to carefully consider the choice of welding processes and consumables, the establishment of comprehensive welding procedures and the need for proper control when storing consumables. During production, it is also important to understand the problems associated with storage, handling and fabrication of stainless steel plates and pipes.

Typical properties for DSS, grade 1.4462 compared to other stainless steel types: As can be seen in table 6, the duplex 1.4462 is 50% more expensive compared to the standard 304L grade in terms of price/kg, but less expensive if we compare Price/PRE and Price/Yield strength, valuable design and service life factors.

The greatest benefit of molybdenum and nitrogen in stainless steels is the improved resistance to pitting and crevice corrosion, especially in environments containing chloride.
One way of measuring this benefit is by determining the critical pitting temperature. Higher PRE means better corrosion resistance. This is normally established with the ASTM G48 test. The critical pitting temperature – CPT – is the point at which pitting corrosion starts in a test specimen immersed in a ferric chloride solution.
Article based on ITW Welding global experience and knowledge.
Tags: CROMAROD, STAINLESS STEEL