Cases
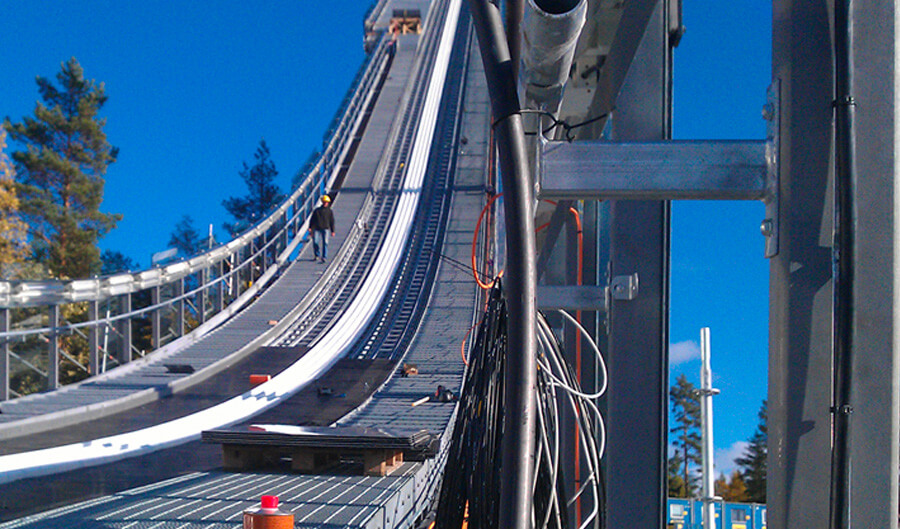
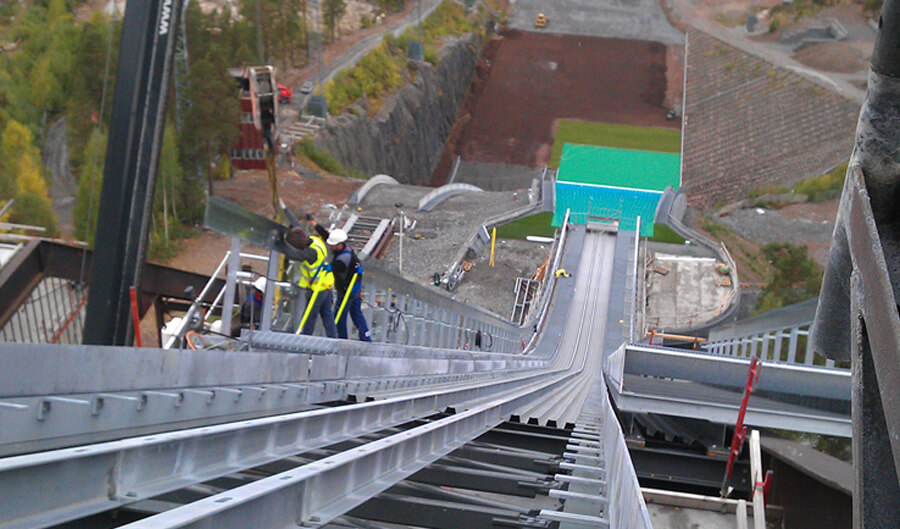
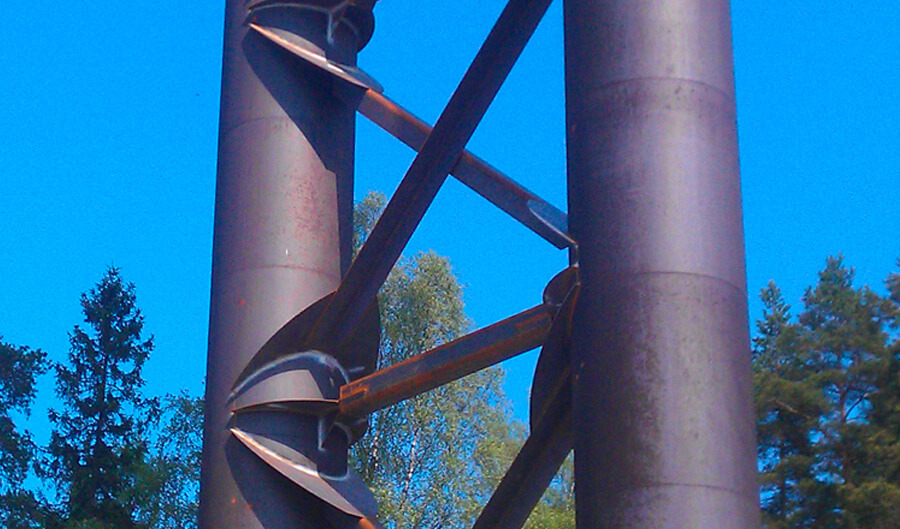
Precision welding from top to bottom
The silhouette is the same. Only a trained eye can see that two entirely new ski jumps at the Lugnet ski stadium in Falun have stood ready since January, 2014. Sjölins Smide in Hudiksvall were busy with the construction welding for just over a year – a job that presented many new challenges Read More
The World Ski Championships were held in Falun in 2015, which was the reason for the two new ski jumps. The old jumps were completed for the 1974 World Championships, and were used for the championships again in 1993. A great deal has happened in the sport since then, and the International Ski Federation (FIS) has entirely new standards for championship ski jumps today. The higher of the two jumps is now a K120 (instead of K115), while its smaller companion is a K90, as before.
Everything is new
“All that remains of the old jumps are the supports and side beams,” said Ulrik Jonasson, MD at Sjölins Smide. “Everything else is new – the tower, the inrun and take off, the stairs and handrails, etc. Previously the jumps were a mixture of wood and steel; today it is steel, concrete and glass.”
Sjölins began the job in November, 2012 and finished in January, 2014. They used almost 200 tonnes of steel.
“It was important that the new jumps resemble the old ones as far as possible,” continued Ulrik Jonasson. “The corten steel gave the old jumps a particular rust-red patina, and the new jumps will look similar, too.”
High-level precision construction
Because the new FIS rules mean that all championship jumps must have the same slope, profile and take off, the inrun on the upper jump has been raised while the lower jump is now longer, shallower and the take-off height has been changed. Achieving the exact profile placed great demands on precision measurement, which was a challenge in itself.
“We began by measuring the jump one spring morning in March,” Ulrik Jonasson told us. “When we began work again after break nothing held true. The sun had heated the structure and moved the measuring points several centimetres. How crazy would it be with fifteen below at night, and plus fifteen during the day? We were forced to decide which readings we would work to, and stick to them no matter what.”
While a lot of work was prefabricated at Sjölins Smides’ workshops, a large amount of welding work was also done on site. To enable installation of the new structures onto what remained of the old jumps, Sjölins welded attachment points for bolted joints with 5 mm tolerances.
“Right at the top of the jumps in the towers the welding was not much different from what we’re used to,” said Ulrik Jonasson. “But the actual jumps slope a lot, so it was tricky work safety-wise and from an ergonomic standpoint. After all, we were sometimes working more than 50 metres above ground.”
Elga and Miller
Sjölins used Elga P 48K electrodes, Elgacore cored wires and Miller XMT 350 welders with feeder suitcases. They performed butt welds and fillet welds in all sorts of positions with 5-20 mm root depths and material thicknesses from 10 to 40 mm. Most was in corten steel, but some was also construction steel. Some areas were covered for MAG welding on site on the jump.
“There’s always low-price materials, but we wanted to be absolutely sure of what we were using and enjoy full back-up all the way,” said Ulf. “For example, Elga helped us with the correct welding parameters, WPSs and welding plans for this particular job. It’s more important to be able to weld efficiently and avoid doing work again than saving pennies on a pack of electrodes.”
Approved by FIS
Our working method was verified by a third-party inspector and Lugnet’s own inspector. When FIS performed the final inspection, it declared that the ski line was according to regulations and within set tolerances.
From horse shoes to steel structures
When Per Sjölin began his farriery and smithy in Hudiksvall back in 1883, he would surely not recognise today’s company. He made the last horse shoe in the 1950s, and today Sjölins’ 75 employees work on structural frame contracts nationwide. It makes steel and stainless steel forgings at its own workshop.
FIS Nordic World Ski Championships
The world championships in Falun began February 18, 2015 and covered cross-country, ski jumping and Nordic combined. In addition to the ski jumps, the National Arena at Lugnet also has cross-country tracks, indoor swimming and arenas for many different sports. The tower for the larger ski jump is open to the public, and is the highest viewpoint in Dalecarlia.
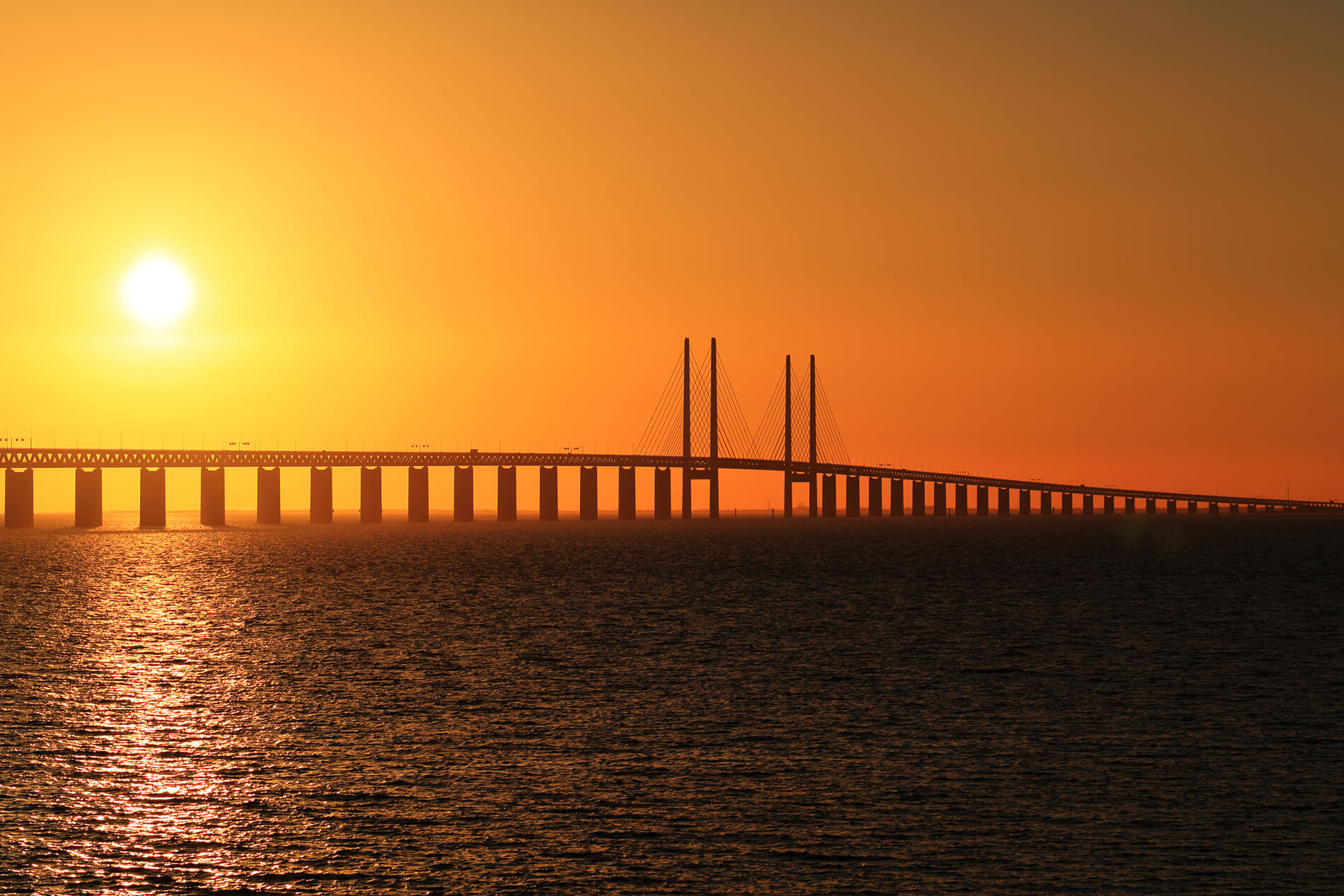
The Øresund Bridge
The Øresund Bridge is the longest combined road and rail bridge in Europe and connects two major metropolitan areas: Copenhagen, the Danish capital city, and the Swedish city of Malmö. Read More
The superstructure of the nearly 8 kilometres long bridge between Sweden and Denmark relies on welds made by Elgacore metal cored and rutile flux cored wires. The superstructure was built in sections by Karlskrona shipyard and was the company’s biggest steel project ever.
Strength and safety
16,000 tons of steel was used to build eight, up to 140 metres long, steel elements. The height is eleven metres, the width 31 and the largest part weighs about 2,000 tons. The superstructure is supported by two pairs of 204 metres high, concrete pylons.
All in all this meant a lot of welding and Karlskrona evaluated a number of consumable suppliers before choosing Elga for this demanding task. Most of the welding was automatic or semi-automatic. The base material was mainly 420 ML and the demands were CVN values at -40°C and CTOD testing at -10°C for thicknesses above 50 mm. High productivity and easy to use were other strong requirements.
From training to follow-up
For automatic and semi-automatic welding Elgacore metal cored wire was used and for manual welding in all positions Elgacore rutile flux cored wire. The metal cored wire was also used for single sided root-runs in dip transfer when necessary.
But Elga’s assignment covered much more than delivering consumables. It also included recommendation of welding parameters, on-site surveys, training of welders and production follow-up.
The Øresund Bridge is a two-level cable-stayed rail and road bridge. It is a part of the link between Sweden and Denmark, and was inaugurated on the 1st of July 2000.
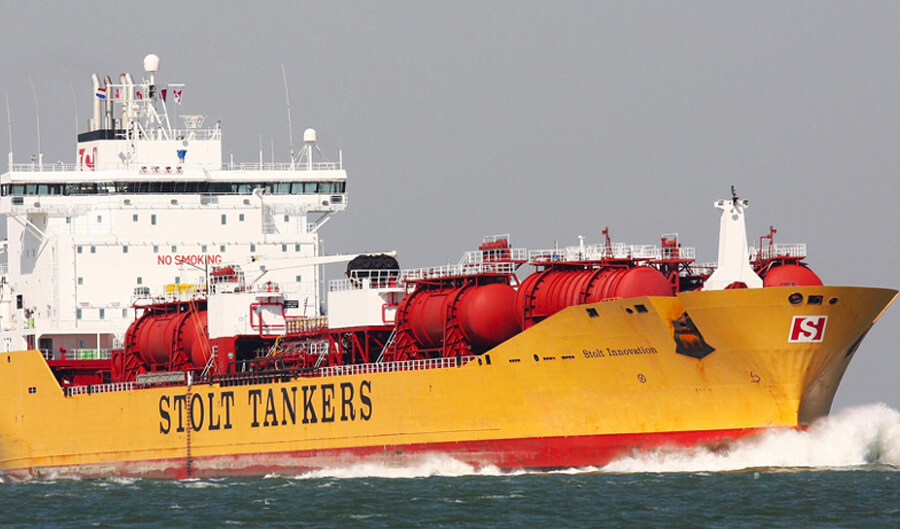
Stainless tankers
For Stolt Nielsen’s Innovation-class vessels, Elga provided not only all consumables for duplex steels but also training programmes and instructors. Read More
The Innovation-class series includes seven chemical parcel tankers built by Danyard. Equipped with 46 duplex steel tanks surrounded by cofferdams, they can carry almost any kind of chemicals.
Elga was chosen to deliver consumables for welding of mild and full duplex steel in the SAW, MMA, MIG, TIG and FCAW processes. We also provided training programmes for engineers, instructors for job training and 24/7 welding specialist at the production line.
An Innovation-class vessel is 176 metres long, 31 wide and weighs 37,000 tons. The cargo capacity is about 40,000 m3.
The Elga consumables used represent most of our range for duplex welding including ceramic backing material.
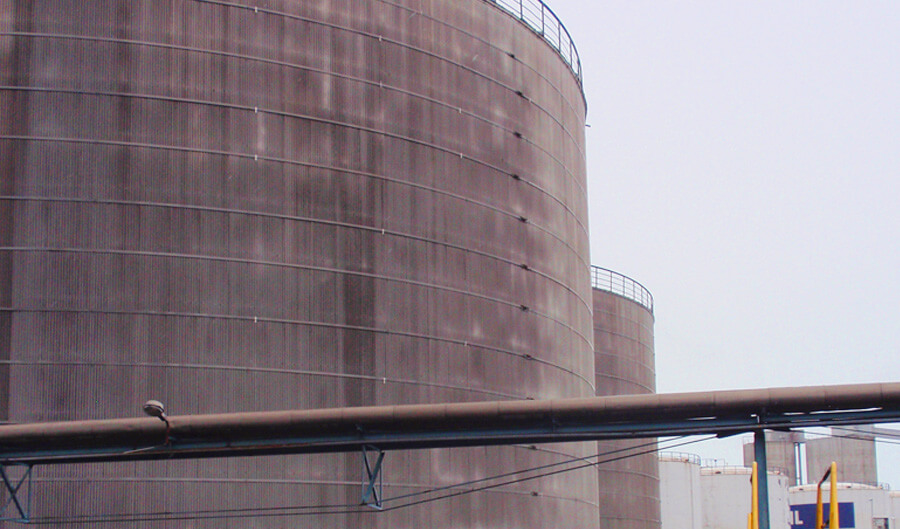
High productivity with flux cored wire welding of LDX steel
"Just as easy as welding ordinary stainless steel but with significantly greater deposition rates than electrodes. This is the first time we've used cored wire for LDX steel and it was an entirely positive experience." Read More
So says Peter Nordell, Project Manager at IVAB in Luleå. The company used Cromacore LDX and Cromarod LDX for re-lining four oil storage tanks in the port of Luleå. The tanks have been empty for several years and needed new floors as they would be used again for storing diesel oil for LKAB.
IVAB worked on the project during the winter and spring of 2012 in tanks that are 35 metres in diameter and 20 metres high. The floors consist of 3 mm LDX steel connected to the shell inside and out. Because of shell thickness (15-20 mm) pre-heating to 150°C was necessary and was carried out using a Miller Proheat 35.
The joints between the floor plates are 5 mm thick and they were welded together using Cromacore LDX flux cored wire. Cromarod LDX electrodes were used for welding on the outside, as these have somewhat better resistance against the elements.
LDX made its breakthrough as an alternative to conventional stainless steel as the latter became ever more expensive due to rising nickel prices. But LDX is not only cheaper, it also has better fatigue properties and is often used in bridges and similar structures.
“The Cromacore and Cromarod LDX consumables have a higher Ni content than the LDX steel to ensure the correct ferrite-austenite balance in the weld,” said Per Sundberg, Product Manager at Elga. “Electrodes have been on the market a long time, but good quality flux cored wire took a while. Cromacore LDX and Cromarod LDX mean we now have a full set of LDX products and I’m confident in saying that the best flux cored wire for LDX welding on the market is Cromacore.”
IVAB’s re-lining assignment on the four storage tanks comprised around 3,000 metres of weld, so maximum welding deposition rate played a major part in the choice of product.
“Flux cored wire provides higher productivity than electrodes,” says Håkan Pavasson, salesman at Elga in Luleå. “Deposition is a full 87 per cent compared to 60 per cent for an electrode, and cored wire requires fewer stops for electrode replacement, which made cored wire very attractive for IVAB. Following an initial test we opted for the cored wire, and despite its being our first time the welding job went entirely without problems.”
IVAB is an installation and pipe fitting company that works with such things as maintenance in process industries and oil installations. Although the head office is in Piteå, the company does business nationwide.