The importance of t8/5 parameter on high-strength steels welding
High-strength structural steel grades have been commonly used for several decades particularly in mobile crane construction.
Recently, the field of applications for high-strength structural steels with yield strength up to 690 MPa has been extended to wind turbine and bridge construction. This trend is because of two main drivers:
-
-
- saving in manufacturing costs and project schedule,
- achievement of the climate goals and the associated reductions in CO2
-
The adoption of steel grades higher than 355 MPa allows designers to reduce the wall thickness of material with considerable savings in structural weight, fabrication time and weld volume to deposit. Overall, it’s less energy and costs of production, storage, transportation and installation.
However, if time and cost saving and related environment benefits are evident, the weak points of designing with higher strength steels are the reduced weldability of such grades, the risk of brittle fracture and fatigue resistance (for welded structures exposed to cyclic loading).
The yield strength that triggers the transition of adopting higher strength steels is 460-500 MPa.
This yield strength represents the current upper limit for steel manufacturers to produce thermomechanical rolling (TMCP) steels.
The main advantage of TMCP steels relies on the extremely fine-grained microstructure obtained through this process with a reduced carbon and alloy content compared to normalised steels of the same grade.
With TMCP steels the weldability is improved overall:
-
-
- lower Ceq content allows lower preheating level,
- lower probability of hard microstructures formation and related Hydrogen Induced Cracking risks,
- higher impact properties and ductility.
-
Quenched and Tempered conditions
Over 500 MPa steels are supplied in Quenched and Tempered conditions. The aim of quenching and tempering is to produce a microstructure consisting mainly of tempered martensite with eventually some amount of bainite. Quenching is performed by rapid cooling of steels brought to 900-960°C down to 300°C by means of a water stream. After quenching the strength is considerably higher but the material too brittle, so a subsequent tempering heat treatment is necessary to increase material toughness.
Welding of steels with strength higher than 500 MPa requires the simulation of the same heat treatment of the parent material (Quenching followed by Tempering). Tempering in welding is “automatically” performed through the multipass technique (every deposited bead tempers the beads of the lower layers) so the critical process is to apply adequate quenching. The temperature-cycle during welding will have a significant effect on the mechanical properties of a welded joint.
The most important reference to define thermic cycle in welding is the t8/5 parameter which is the cooling time of heat affected zone between 800°C and 500°C. At 800°C, the transformation starts from austenite to martensite (Ms) and at 500°C it finishes (Mf).
Estimation of t8/5 parameter
In EN 1011-2 two formulas are defined for the estimation of t8/5 parameter as a function of heat input, preheating temperature, combined thickness and geometry factor (two-dimensional or three-dimensional heat flow).
The two main key variables in the t8/5 calculation are heat input and preheating/interpass temperature.
Increasing heat input and preheating temperature will lead to longer cooling time and consequently to lower strength and toughness (grain coarse effect). On the other hand, decreasing heat input and preheating temperature will lead to increase the hardness with the risk to introduce cracks (depending on the diffusible hydrogen level).
A limitation of the t8/5 to the upper and lower value is necessary to obtain good mechanical properties in the weld and in the HAZ.
The optimal t8/5 window becomes narrower with increasing yield strength. For 690 grade cooling time between 5 and 15 seconds typically allow to achieve acceptable mechanical properties.
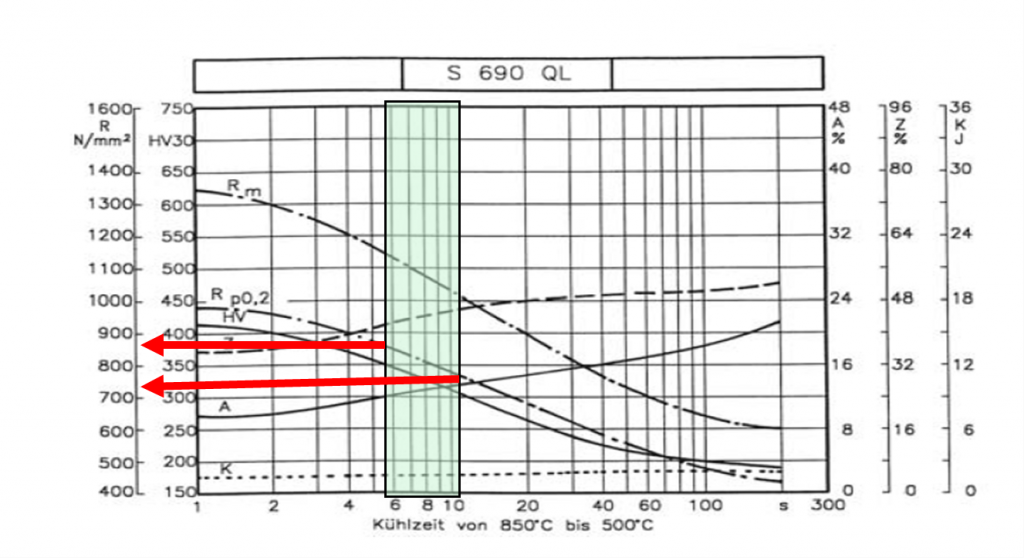
Calculating the minimum preheating temperature
EN 1011-2 allows also to calculate the minimum preheating temperature in normal constraint conditions as a function of heat input (Q), chemistry (through carbon equivalent CET), plate thickness (d) and diffusible hydrogen (HD):
For a given CET, thickness and heat input the above formula shows the influence of diffusible hydrogen on the minimum level of preheating required to avoid cold cracking risk.
Optimal weld parameter box
Minimum and maximum t8/5 and Tp can be finally combined to define an optimal weld parameter box (Falko Schröter, Ronny Willms “Welding and fatigue in high performance steel”):
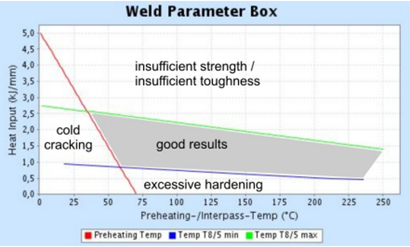
For t8/5 above the green line (t8/5 max) the risk is to not achieve the required tensile and impact properties (too slow cooling cycle, grain course effect).
For t8/5 below the blue line (t8/5 min) the risk is to get martensite metallurgical structures (too fast cooling cycle, risk of brittle fractures).
Higher diffusible hydrogen levels would shift to the right the red line (Tp min) reducing the width of the “good results” region.
Tags: FCAW, MCAW, MEGAFIL, Problem Solving, Stick Welding, Welding