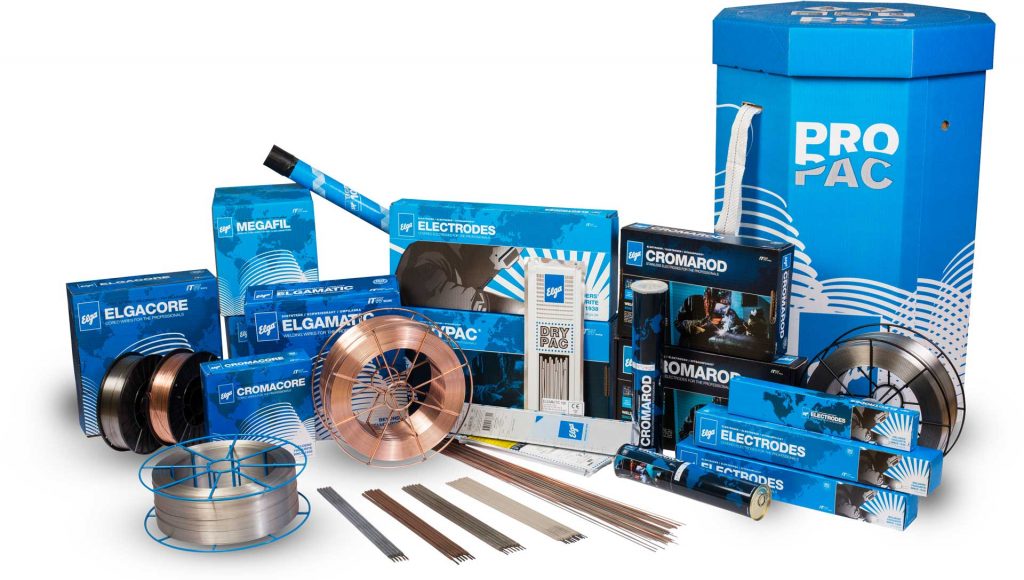
If filler metals become wet or pick up contaminants from the job site, such as dirt, oil, grease, or other impurities, they simply and without question need to be replaced. That replacement leads to three costly problems. One, it causes downtime for changing over the filler metal, particularly welding wires. Two, filler metal damaged by the environment almost always voids most industry-standard one-year warranties on the product. Three, it costs the contractor money—for both the price of the ruined filler metal and for the purchase of new filler metals. These are a trifecta of problems and costs.
Time for Damage Control
When filler metals leave the factory, they are sealed (usually vacuumed, hermetically, and/or placed in a heavy plastic bag or wrap) and in the best possible condition for the job. It’s then the contractor’s responsibility to keep them that way, regardless of the harsh job site conditions. Fortunately, there are some relatively easy steps they can take to help them accomplish this task.
First, contractors should always use gloves when handling filler metals. Solid wire, in particular, can easily pick up sweat from bare hands. This moisture causes rust to form on the surface of the wire, which in turn leads to poor wire feeding and may create porosity in the finished welds. Contractors can usually tell through a visual inspection of solid wire if it’s been damaged in this way: the rust mark will often be in the exact shape of a handprint! Other types of filler metals won’t show such telltale signs of improper handling, but it is nonetheless important to wear gloves when removing them from their original packaging or preparing them for welding.
Because plasma and oxy-fuel cutting create a significant amount of dust, these processes, which are both common on the job site, should be kept clear of filler metals. The cutting dust can accumulate on the surface of flux-cored and solid wires, and cause poor wire feeding. Cutting dust can also clog the contact tip and nozzle in these applications, creating poor electrical conductivity and an unstable or erratic arc. In a stick electrode application, dust can lead to weld porosity. For all of the aforementioned reasons, it is a good practice to keep cutting activities in a separate area from where welding occurs.
Contractors should also keep filler metals away from water, oil, grease or other similarly damaging elements. These contaminants can all lead to poor weld quality, rework and/or welding performance issues that negatively affect productivity on the job site. Moisture, especially, can cause hydrogen-induced cracking that must be repaired.
The single most important practice a contractor can implement on a job site, however, is to properly store filler metals when they are not in use. First, when flux-cored welding or MIG welding with solid wire, contractors should cover the welding wire spool with a plastic bag if they plan to leave it on the wire feeder overnight. That is the least they should do.
A better practice involves a few more steps but it is worthwhile to avoid potential welding wire contamination. At the end of the workday, remove the spool from the wire feeder, place it in a clean plastic bag and close it securely. Then place the secured package into the original box and store it in a clean dry area until it is ready for use again.
As a side note, using an enclosed wire feeder, when possible, is also a good way to protect flux-cored wire and solid wire from harsh job site environments. Still this type of feeder will not prevent damage to the filler metal surface if the welding wire is left in the enclosed feeder for any length of time. Contractors should still follow proper handling storage procedures.
Stick electrodes also require proper handling and storage on the job site if contractors are to achieve proper weld quality, maintain compliance with the specified welding parameters and eliminate unnecessary downtime.
Without question, moisture is the number one enemy of stick electrodes—it can cause hydrogen induced-cracking, porosity and a host of other weld discontinuities that require rework. Depending on the type, stick electrodes must often be stored in a holding oven at a specific temperature (See Figure 1 above) to protect them from moisture. In some cases, a specific welding procedure or code even dictates how long a package of stick electrodes can remain open before it must be discarded—regardless of whether it has been stored in an oven or not.
Not surprisingly, leaving a package (can or carton) of stick electrodes open and/or storing it improperly during or after the workday are the biggest mistakes contractors can make on the job site, especially with low-hydrogen products. Contractors should always follow the welding code specifications for the job, as well as the filler metal manufacturer’s instructions for the particular stick electrode. Proper oven storage or holding temperatures are key. Contractors should also look for packaging options that provide greater moisture resistance, such as vacuum pack DRYPAC® or hermetically-sealed metal can, and always close the package after retrieving an electrode.
In the event that stick electrodes have been exposed to moisture, contractors should follow the recommended procedure for reconditioning them. Reconditioning involves placing the damaged electrodes in an oven at a given temperature for a specified period of time. Instructions for reconditioning are included with the original stick electrode package, or can be determined by contacting a trusted welding supply distributor.
Note welding wires should never be reconditioned.
A Small Price to Pay
Most contractors would likely agree that filler metals are only one of many concerns they have on a job site. Worker safety, compliance to the job specifications, material handling, and other job site issues certainly take precedence. Still, the goal of any job is to complete it correctly, on time, under budget, and with the greatest amount of efficiency. Properly handling and storing filler meals can be a simple way to help make such goals a reality. It just takes a little time and know-how to yield positive results—both in cost savings and productivity.
Article based on ITW Welding global experience and knowledge.
Tags: DRYPAC, Problem Solving, PROPAC, Welding