Stainless steel is not a specific material, but a common term for a group of corrosion-resistant steel types. Stainless steels are steels which normally have a chromium content of at least 10.5%.
They can also contain nickel, molybdenum, nitrogen, copper, manganese, tungsten, titanium, niobium, cerium and other substances in varying degrees. Interest in nitrogen as an alloying element is increasing and many stainless steels, both austenitic and duplex with significant nitrogen levels have been in commercial use for the last ten years. It is well demonstrated that nitrogen in combination with molybdenum significantly increases resistance to pitting corrosion. The nitrogen also increases yield strength by solid solution strengthening of austenite.
Since the mechanical properties and the usefulness of each type of steel is dependent on its composition, it is important to take into account the different qualities of each type before choosing the steel and welding consumable for the application concerned.
Metallurgy
Alloying elements are usually divided into two groups – austenite stabilizers and ferrite stabilizers – as shown in table 1. Some alloying elements used in stainless steels are described in table 2.

Stainless steels are divided into four subgroups:
- Ferritic stainless steel
- Martensitic stainless steel
- Austenitic stainless steel
- Duplex stainless steel

Increasing the amount of austenite stabilizing elements or decreasing the amount of ferrite stabilizing elements will therefore promote a fully austenitic structure. In the same way, an increase in ferrite stabilizing elements or a decrease in austenite stabilizing elements would promote the ferritic phase.
Consider the phase diagram for Iron-Chromium-Nickel as shown in figure 2. Note that if we follow the composition 22% Cr-10% Ni (A) during cooling from liquid to room temperature, the first phase formed is delta. This is a ferritic phase also called delta-ferrite. At about 1400 °C, the melt is fully solidified and the phase present is delta-ferrite. Below this temperature, some of the delta-ferrite will be transformed to the gamma phase. Gamma is an austenitic phase which, compared to delta-ferrite, is non-magnetic.
If the composition of the melt had been 17% Cr-15% Ni (B) instead, the gamma phase would have formed initially. Below 1400 °C, the only existing phase is gamma and the steel is fully austenitic. By adding elements shown in table 2, it is possible to control which phase is formed and in which amount it is present.

For welding applications, it is often desirable to have a small amount of delta-ferrite in the weld metal. The reason for this is that ferrite has a higher solubility for sulphur and phosphorous than austenite. Primary austenite solidification causes Atmospheric corrosion resistance as a function of chromium content rejection of sulphur and phosphorus to the remaining liquid. A low melting point segregates results, which become trapped between growing dendrites (austenite grains) causing cracks along grain boundaries. Primary ferrite solidification does not cause sulphur and phosphorus rejection, thus preventing solidification cracking.
Sometimes, however, it is not desirable to have any delta ferrite at all. This is the case in high temperature applications, where delta ferrite during service will transform to the very brittle sigma-phase causing weld metal embrittlement. Type 310 fully austenitic steel is often used in such applications.
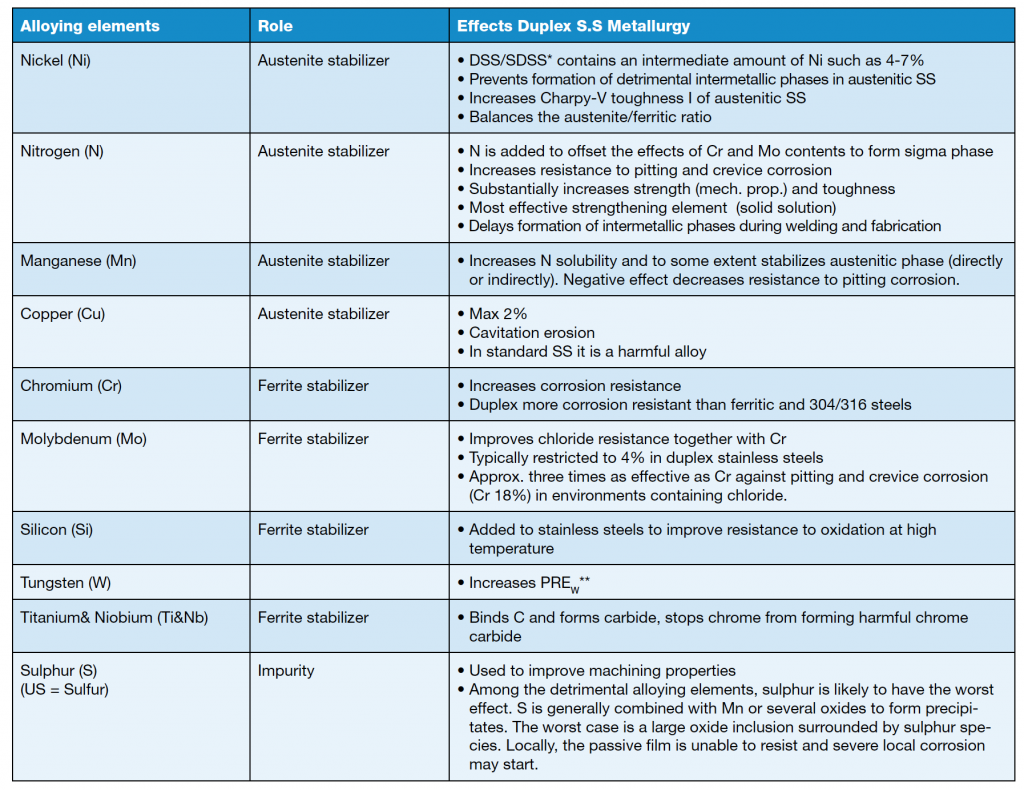
Corrosion resistance
A characteristic common to all stainless steels is that they contain chromium (min 10.5%), which inhibits corrosion. This excellent resistance results from the naturally occurring, chromium-rich oxide layer which always exists on the surface of stainless steel. This oxide layer has the unique property of self-healing, which cannot be achieved with layers applied by other means.
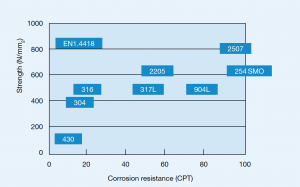
If the oxide layer is removed or damaged by abrasion, or if the raw metal surface is exposed when the steel is cut, a new layer is immediately formed by reaction between the steel and the atmosphere or other sources of oxygen. Because protection is re-established immediately, it is possible to choose steel that is not affected even in aggressive marine environments, or by many acids, alkalis and other chemicals.
Strength and formability
Stainless steel is sometimes cold stretched to increase strength, mainly for pressure vessels. Also in the embodiment, the tensile strength of the original stainless steel exceeds that of carbon steel. Similarly, hardness also varies from relatively soft annealed austenitic stainless steel to extremely hard martensitic materials, particularly for razor blades and ball bearings.
In general, ductility is inversely proportional to strength. Soft austenitic steels have outstanding ductility with an elongation exceeding 50%. Austenitic stainless steels can be cold worked to form a large number of semi-finished and finished products. Cold working can be optimized so that the final product achieves the best combination of strength and hardness. Ferritic stainless steels offer good strength and ductility, but without the outstanding formability of the austenitic variants. Martensitic steels can be formed in the annealed condition and subsequently heat treated to achieve the required strength and hardness.
Temperature spectrum
Stainless steel discolours if heated to very high temperatures, but this does not lead to scaling as in ordinary carbon steel and it retains much of its strength when heated. Consequently it is used in industry for many applications where durability at high temperatures is vital.
Strength decreases when steel is heated. The extent of the reduction is dependent on many factors, one of the most important being the actual alloy composition. Compared with carbon steel, stainless steel retains its strength when heated. Therefore, it is used in high-temperature environments in industry for its so-called creep strength and is chosen by many designers thanks to this characteristic.
High-temperature corrosion (scaling) must be avoided, although heat-resistant stainless steels are superior in this regard, because they are stable in contact with air and most of the products of combustion in temperatures up to +1100 ºC. A lot of industrial processes are performed at very low temperatures, down to -196 ºC (or even lower), and at such temperatures many materials lose their ductility and toughness and fail by brittle fracture. In such applications, specific austenitic stainless steels or nickel alloyed steel are ideally suited.
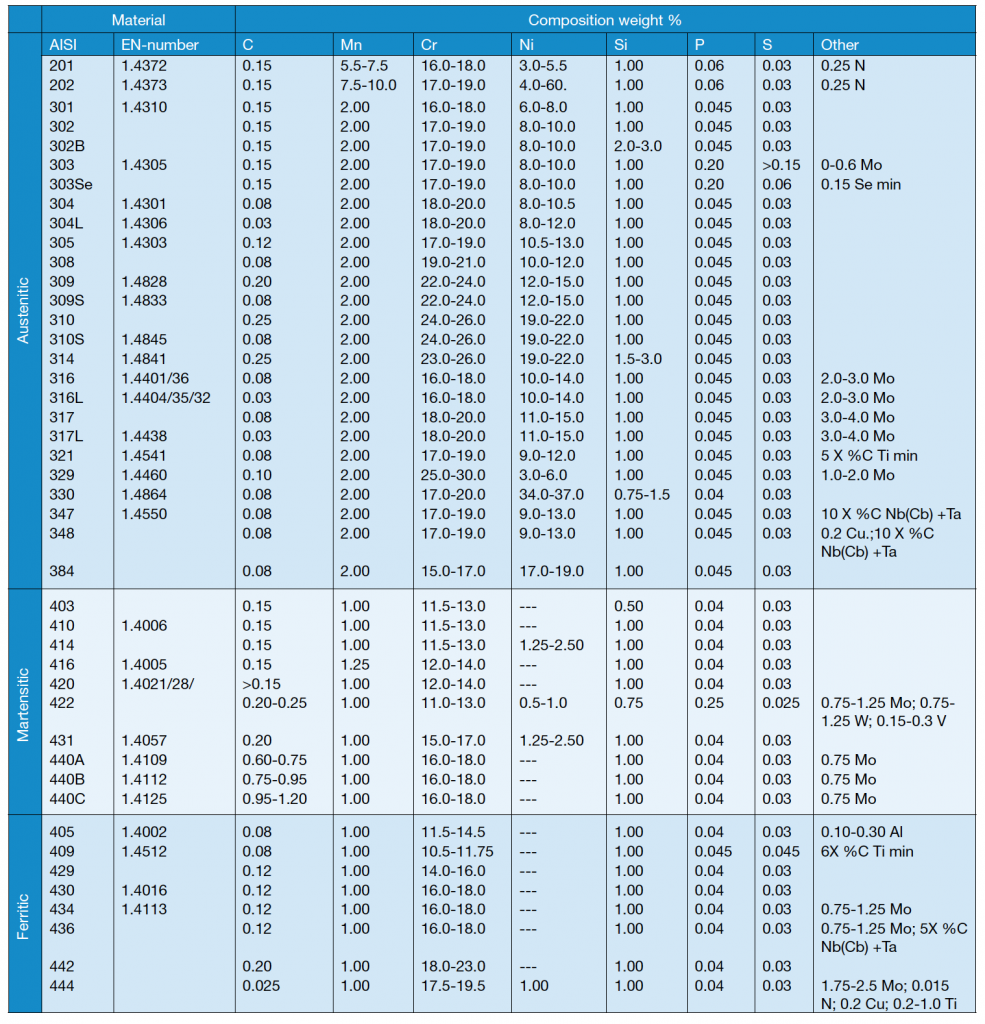
Several austenitic steels in table 3 contain about 18% Cr and 8% Ni and are often known by the popular term 18-8 stainless steels. Types 304 and 304L are very common grades and differ only in carbon content.
The ‘L’ grades are designed to avoid sensitization (Cr depletion close to grain boundaries due to chromium carbide formation) which can result from the heating cycle during welding. 316 and 316L contain additional molybdenum, which improves strength at high temperatures but most of all reduces the risk for intergranular corrosion.
The 347 type is known as stabilized stainless steel. This steel is used for elevated temperature applications, where a higher carbon content than that found in 304L and 308L is necessary to achieve good creep resistance. To avoid problems with chromium depletion as mentioned above, steel has to be stabilized. This is done by the addition of niobium (or columbium) and tantalum, which are strong carbide formers (stronger than chromium).
Article based on ITW Welding global experience and knowledge.
Tags: CROMAROD, STAINLESS STEEL, Stick Welding